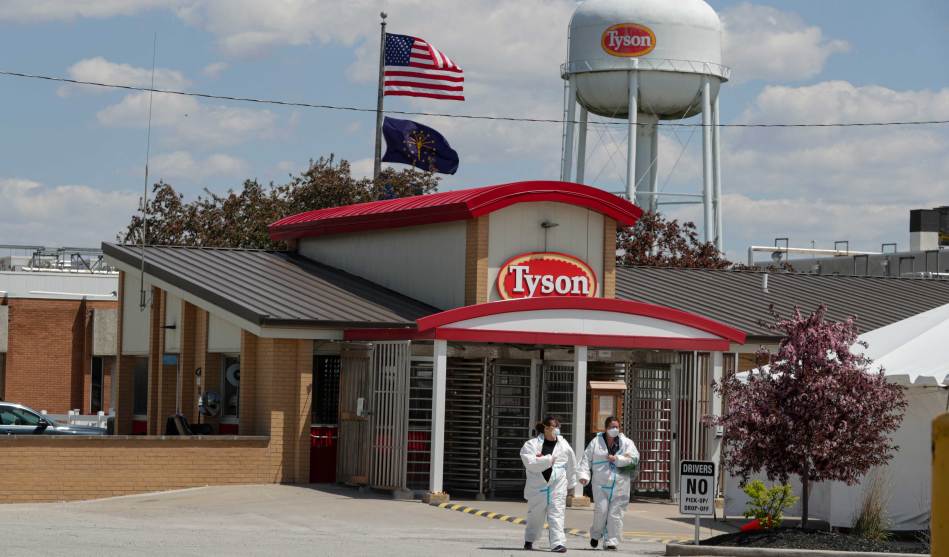
Michael Conroy/AP
This story was produced by the Food & Environment Reporting Network, a non-profit news organization.
In late April, around the time that President Donald Trump signed an executive order declaring US meatpacking plants to be “critical infrastructure” in an effort to keep them open after they emerged as coronavirus hotspots, Germany’s slaughterhouses reported their first cases of the virus. In the ensuing weeks, as the number of cases in Germany’s meat plants has climbed to at least 989, according to media reports and information from trade unions, the response from government has been strikingly different than in the United States.
While Trump’s order was widely seen as an appeasement of the meat industry, one that took decisions of whether to close plants with coronavirus clusters out of the hands of local officials, the German government has come down on the side of the workers. Its labor minister expressed shame over the precarious living and working conditions for slaughterhouse employees and vowed “to be led not by lobbying interests but by the public good.” The cabinet has proposed a series of reforms that would increase regulation of the industry and transform its labor practices, analysts say, though they face strong opposition from industry groups.
The contrast in these official responses is perhaps the starkest example of how differently the coronavirus crisis in the meat industry is playing out in Europe and the United States. But it’s not the only one. More than nine times as many meat industry workers have tested positive for coronavirus in the United States than in Europe – and dozens more American workers have died – according to figures from governments, media reports and unions, though the U.S. meat industry employs only a third more people.
While American meatpacking plants have been allowed to reopen after outbreaks, without testing all workers, two German states have begun testing virtually all slaughterhouse employees. France’s Agriculture Minister is considering testing every abattoir worker in the country after 115 workers tested positive in recent weeks. And, while JBS USA, the American branch of the world’s largest meat company, threatened to take legal action against union members who spoke out about conditions in its Greeley, Colorado, beef plant where six employees have died, workers at one of the company’s chicken processing plants in Northern Ireland walked off the job in March and won new protections.
To be clear, Europe’s meat processing plants and slaughterhouses are not coronavirus-free zones. Outbreaks, particularly in Germany, the UK and Ireland, have cast light on exploitative working conditions and insufficient safety measures. And yet, without minimizing the situation in Europe’s meat industry, it’s clear that the problem is far more contained than in the United States. While no single factor explains this discrepancy, union officials, academics and market analysts all say that differences in baseline worker protections, the ways the industry is structured, and the political response to the virus are likely at play.
The European Union’s meatpacking industry employs 350,000 people about two-thirds the number of US workers. Yet European meatpackers have had only a fraction of the coronavirus cases that have swept US plants and far fewer deaths. As of June 9 in the United States, at least 24,715 meatpacking workers have been infected with Covid-19 and at least 86 have died, according to data collected by the Food & Environment Reporting Network’s Leah Douglas. In European slaughterhouses and meat processing plants, at least 2,670 coronavirus cases have been reported and four workers have died, according to an analysis of news reports, government figures and union statistics. The bulk of cases are in Germany and Ireland, but Spain, England, Northern Ireland, France, Italy and The Netherlands have all had outbreaks.
Josef Schmidhuber, deputy director of the trade and markets division at the United Nations’ Food and Agriculture Organization, says he expects that the number of cases in European slaughterhouses has not yet peaked, but also “strongly doubts” that it will reach the proportions seen in the United States.
The American and European meat industries have a fair amount in common. Slaughterhouse employees in both work close together and social distancing is difficult. Both rely heavily on immigrant labor. In German slaughterhouses, for example, foreign-born workers—mostly from Eastern Europe and employed by contractors—make up somewhere between 60 and 80 percent of the workforce, and there are longstanding concerns about the conditions in which they labor. The meat industries in both the United States and Europe also are highly consolidated, especially in Germany, which is the third largest pork producer in the world after China and the United States. Three out of every four pigs slaughtered in Germany are processed by the country’s four largest meat companies.
Despite these parallels, Schmidhuber points to a major difference between European and American slaughterhouses: their size.
In Europe as a whole, and even in the pork powerhouse of Germany, slaughterhouses are much smaller on average than US plants, though they’ve grown steadily over the years. The region does have a small handful of very large slaughterhouses, but even those are still not as big as their supersized American counterparts. This means that even if an infection runs rampant through a facility, the ultimate number of cases is generally limited. Schmidhuber cited, as an example, a recent outbreak of Covid-19 in Dissen, Lower Saxony, where 278 workers were initially tested and 92 were found to be positive.
“Two hundred and seventy eight employees? That’s not even the back office of the Sioux Falls plant,” he said, referring to a Smithfield Foods plant in South Dakota that employs 3,700 employees, where two workers have died and 853 have tested positive.
With slaughter operations spread across smaller plants, German meat companies have been able to close individual facilities with coronavirus cases and shift production to other locations. “You don’t reap the same economies of scale,” Schmidhuber said, “but you are more resilient to shocks like Covid-19.”
So far, there’s been no sign of the sort of meat shortage like the one underway at US grocery stores, says Tim Koch, an analyst at the German agricultural market research firm AMI. “We have plenty of meat for sure,” he says, though he noted that could change if a larger share, like 20 to 30 percent, of German slaughterhouses were to close.
Line speed is another factor. American meat workers aren’t just working in larger facilities, they are often working faster than their European counterparts, too, says James Ritchie, assistant general secretary of the Geneva-based International Union of Food, Agricultural, Hotel, Restaurant, Catering, Tobacco and Allied Workers’ Associations, a federation of 427 trade unions from across the world.
Slaughter line speeds have long presented major concerns for worker health and food safety in the United States, where some employees have resorted to wearing diapers because they don’t have time for bathroom breaks, Ritchie says. Those conditions could make it impossible to comply with coronavirus precautions, he said: “You can’t even stop to cough into your hand or your elbow because the line speeds are so, so fast.”
In the US, line speeds are set by the federal government, though the meatpacking industry has long pushed to have these limits lifted or abolished altogether. Despite repeal attempts, the pork line speed limit stands, for now, at 1,106 hogs per hour (though a handful of plants have opted in to a new system that does not limit line speeds). For broiler chickens, it’s 140 birds per minute, though an increasing number of plants have gotten exemptions that allow lines to process up to 175 birds per minute—which translates to 10,500 birds per hour.
There are no Europe-wide speed limits of this sort; it is left to authorities in individual countries, or even states, to set limits, which means they can vary tremendously and data are difficult to obtain. Overall, though, slaughter lines in much of Europe are slower. Ireland’s pork plants slaughter between 20 and 450 pigs per hour, according to its Department of Agriculture, Food and the Marine. Antoni Dalmau, a researcher at the Institute of Agrifood Research and Technology in Spain who studies animal welfare, said that, on average, most European pork plant lines operate at around 400 pigs per hour, with the larger plants slaughtering around 800 to 900 per hour. European poultry lines run at around 6,000 birds per hour on average, Dalmau says, though much faster facilities slaughtering at much quicker speeds exist, including in Ireland, where the swiftest process 14,000 chickens per hour.
In addition to differences on the slaughterhouse floor, Kristjan Bragason, the general secretary of the European Federation of Food, Agriculture and Tourism Trade Unions, points out that general working conditions in Europe, where paid sick leave and health insurance are mostly a given, may have also helped sick workers feel secure enough to stay home and self-confine. “The pressure to go to work is not the same as in the US,” he said.
Furthermore, unions and large companies are largely in agreement about coronavirus safety protocols, Bragason said. His union and the sector’s largest industry group, Food Drink Europe, for example, have jointly issued Covid-19 safety guidelines for food processing facilities.
When there have been outbreaks, European industry and safety regulators have generally reacted quickly. “I think that what should have happened in the U.S. and I think is generally happening in Europe is that as soon as there is a case discovered in a meat-processing plant, it’s shut down, test, trace, isolate, quarantine, disinfect,” Ritchie said.
But proactivity and precautions have only gone so far. Workers in Northern Ireland and Spain, for example, have accused companies of not taking proper precautions even after cases of the virus were discovered.
At JBS USA’s Moy Park chicken processing plant in Portadown, Northern Ireland, workers were concerned the company was moving too slowly in putting safety measures, like plexiglass dividers, in place. And as the demand for chicken spiked when restaurants closed, the company contracted new workers, mostly immigrants who didn’t speak English and received little training, according to Sean McKeever, a representative for Unite, a union that represents workers at the plant. “They marched them into the factory and told them to pack boxes,” he says. “They weren’t shown how to wash hands, there wasn’t any social distancing. These people hadn’t a clue. These are very vulnerable people.”
The workers left the plant for 15 minutes. To get them back on the line, the company increased pay by 30 pounds a week (about $37) and began offering workers a parcel of meat to take home each day. But the most important thing was that the company quickly put into place the protective measures and training that the workers demanded.
Even though many German companies increased sanitary procedures and started taking the temperatures of workers every day, before any cases appeared, they failed to consider their workers’ housing and transportation situations, Koch said. That was a crucial mistake. The contract workers live in crowded, barracks-like conditions that are largely being blamed for the outbreaks. Still, Schmidhuber pointed to “a fundamental difference” in the German meat industry’s response to that of U.S. companies. In mid-May, the meat producer Tönnies released a 14-point plan to respond to the crisis. This includes ending the practice of housing more than 10 workers together, increased coronavirus testing and establishing an early warning system in cooperation with local authorities.
And if these measures were in part an attempt to stave off further regulation, it may not have worked. The new rules proposed by the German cabinet would outlaw subcontract work arrangements in the meatpacking industry, double the maximum penalties for employers that violate limits on working hours, and mandate more government oversight of worker housing. While this slate of reforms still needs to be approved by Parliament, it would bring about sweeping changes in the industry that would persist after the coronavirus epidemic ends. Still, agriculture industry groups and their allies in government are pushing back against the proposal, saying it goes too far and could put the industry at risk.
Yet even as the number of coronavirus clusters ticks upward in European slaughterhouses, the crisis in U.S. plants stands as an example of how bad things could get if the problem isn’t handled correctly.
McKeever, who continues to push for safety improvements at a number of Moy Park’s other operations, often invokes the specter of U.S. hotspots. He says he hopes that the coronavirus epidemic will mean more respect and better conditions for meatpacking workers and other low-wage employees on the front lines on both sides of the Atlantic.
“We have our nurses and doctors saving lives and we have these vulnerable people feeding the nation,” he said. “I think what this may well do going forward is to make us really look at the value that we put on some of these people who are so essential to our way of living—not solicitors, not some consultant, not some senior manager at a big conglomerate, but these people. If we didn’t have these people, we wouldn’t be able to feed ourselves.”
*This story has been corrected to show six deaths have been confirmed at the JBS plant in Greeley, Colorado, not 12. The total number of US meatpacking workers who have died has also been updated to 86, reflecting that change.